改善提案に迷ったら?製造業20代~30代が押さえるべき改善の進め方
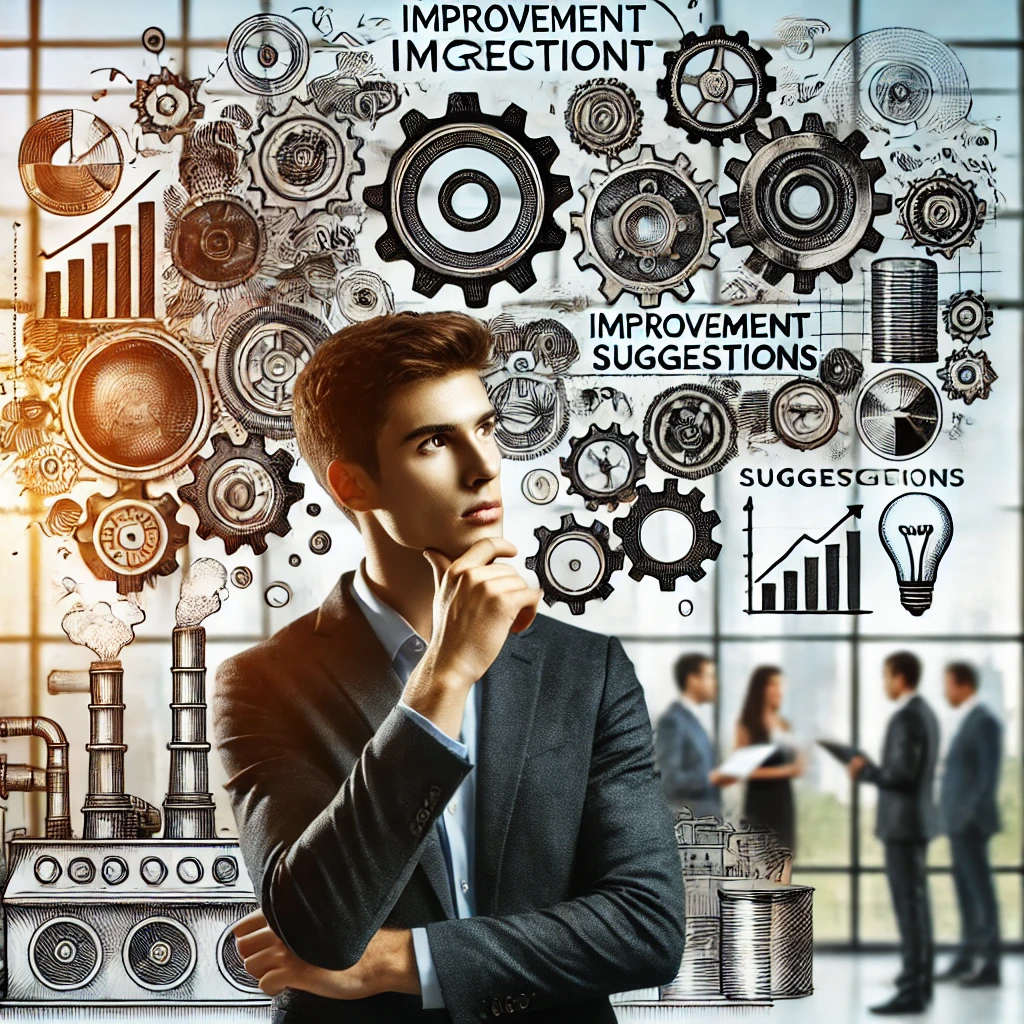
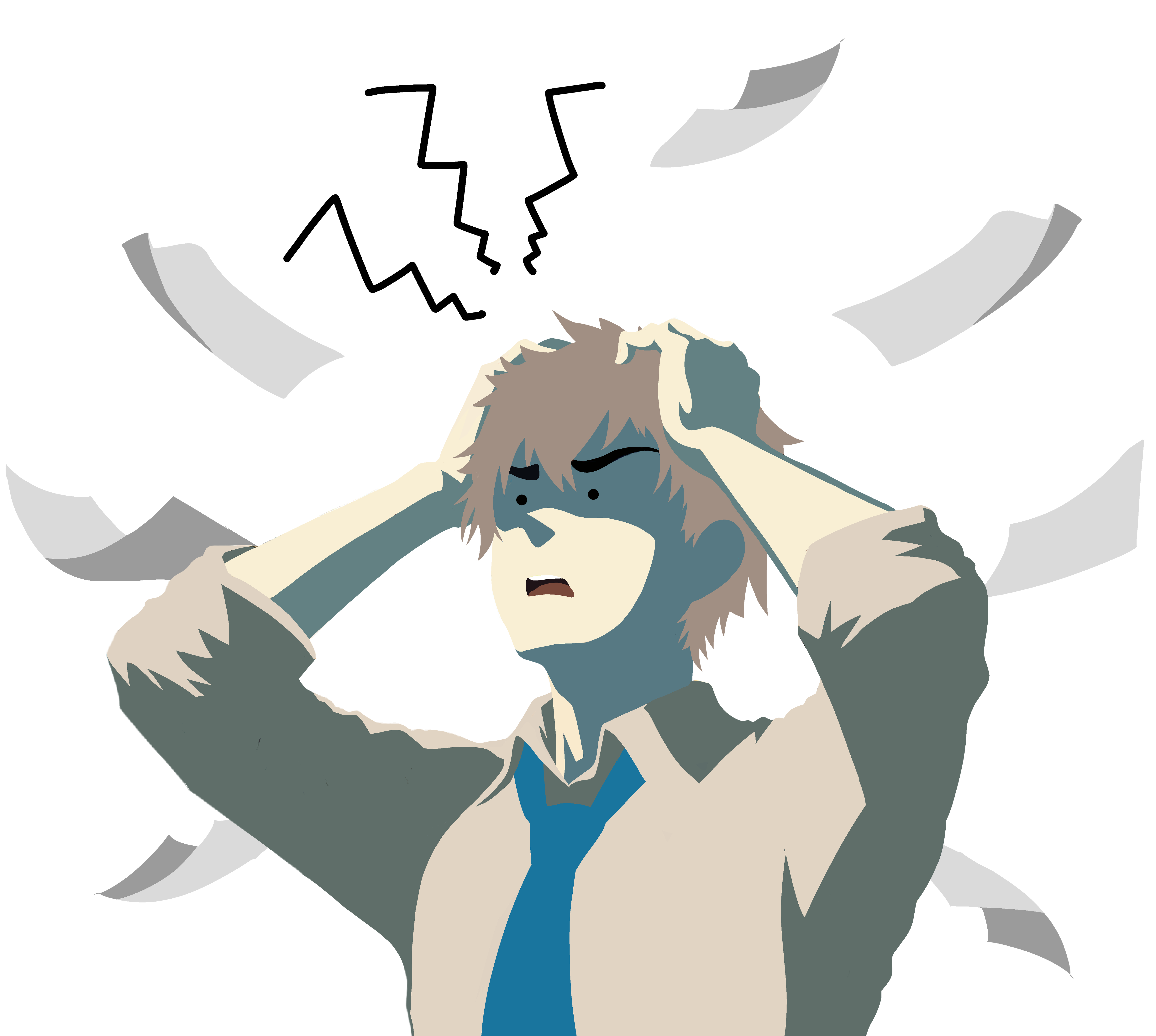
改善提案月に1つ出すように言われているけど何を改善したらいいかわからくて出せないよ!!!!
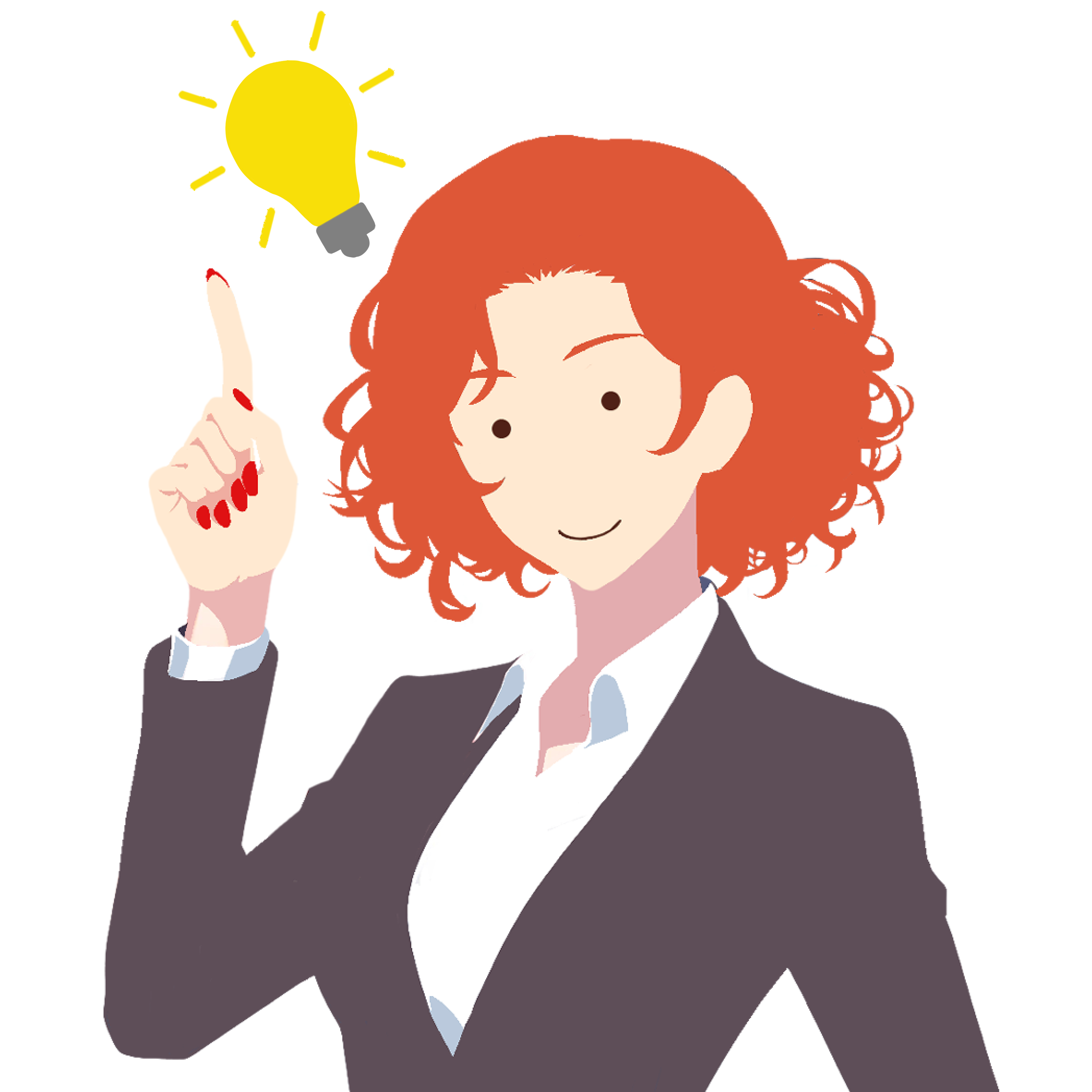
毎月改善することは大変なことです。
少し見方を変えるだけで改善のネタはたくさんあります。
中小企業製造業の20代~30代前半向けに、改善提案の悩みを解決する考え方を学びます。
改善の重要性や見つける方法を解説し、働きやすい環境づくりに役立ててください。
改善に取り組むことが難しいと感じている20代~30代前半の製造業の方必見!
この記事では、あなたの興味関心に応える改善の考え方や見つけ方をわかりやすく説明します。
改善をする上でのキーワードを先に紹介しますそれは
「めんどくさい」です。
この「めんどくさい」と感じることが多くの改善を生みます。
最後まで読むことで、あなたの悩みが解決されるだけでなく、改善活動を行う上での効率や業務品質への向上も実現できるはずです。
改善とは
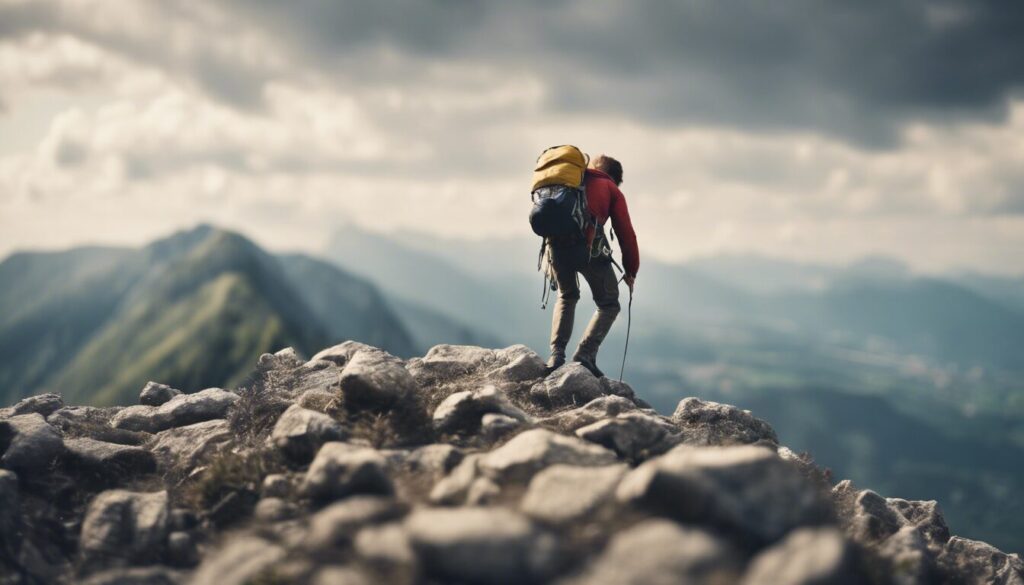
改善とは、ある状態や環境をより良いものにする取り組みです。
企業においては、生産効率や品質、業務の効果を向上させることを目的とします。
具体的な例として、作業工程の短縮や品質管理の強化が挙げられます。
また、現場の声を取り入れ、問題解決に繋げることも重要です。
一方で、個人レベルでも日常生活や職場環境の改善に取り組むことで、ストレスの軽減や効率アップが期待できます。
改善活動には、PDCAサイクル(Plan:計画、Do:実行、Check:評価、Act:改善)がよく用いられます。
(PDCAはほとんどの企業で聞く言葉だと思うので覚えておいてください。)
このサイクルに沿って計画的に取り組むことで、より効果的な成果が得られるでしょう。
さらに、改善活動を成功させるためには、経営層と社員全体が連携し、問題意識を共有することが不可欠です。
企業が取り組む改善策の一部には、5S(整理、整頓、清掃、清潔、躾)やカイゼン活動、リーン生産方式などがあります。
無駄を徹底的に排除したスマートな生産方式のこと。
改善の重要性
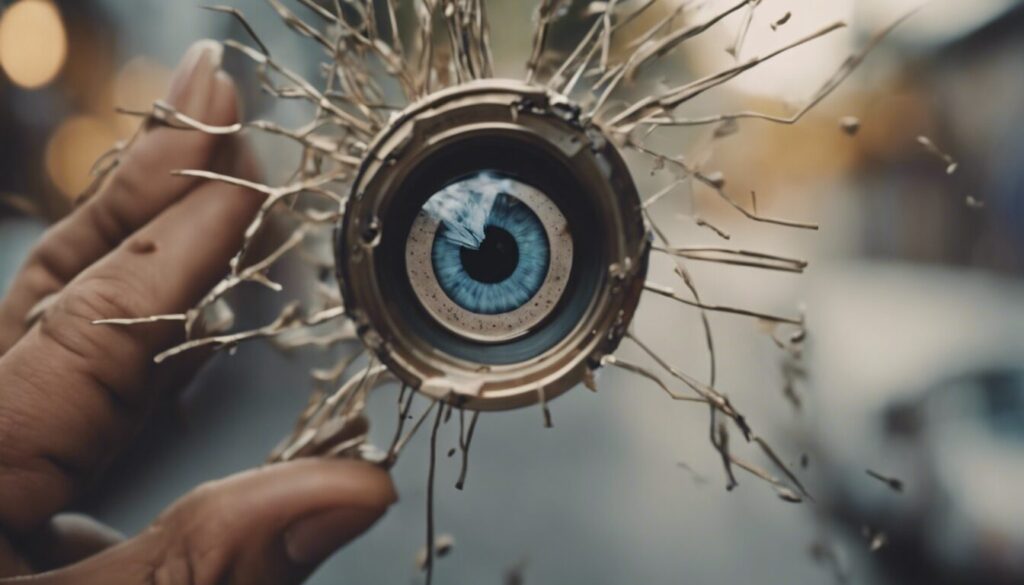
特に製造業において、改善活動の重要性は高まっています。
事例としては、生産ラインの効率化や品質向上、環境負荷の低減が挙げられます。
これにより、企業は競争力を維持しつつ、新たなビジネスチャンスを掴むことができます。
また、改善は小さいことから始めることが重要です。
例えば、作業現場における無駄の削減や、効率的な業務プロセスの見直しがあります。
徐々に積み重ねることで、大きな成果に繋がります。
さらに、改善活動によって、社員の能力開発やスキルアップ、チームワークの向上にも寄与します。
これは、企業としての持続可能性を向上させる要素となります。
したがって、改善活動は企業にとって必要不可欠な取り組みであり、小さなことからコツコツと着実な成果を上げることが大切です。
改善することで自分へのメリット
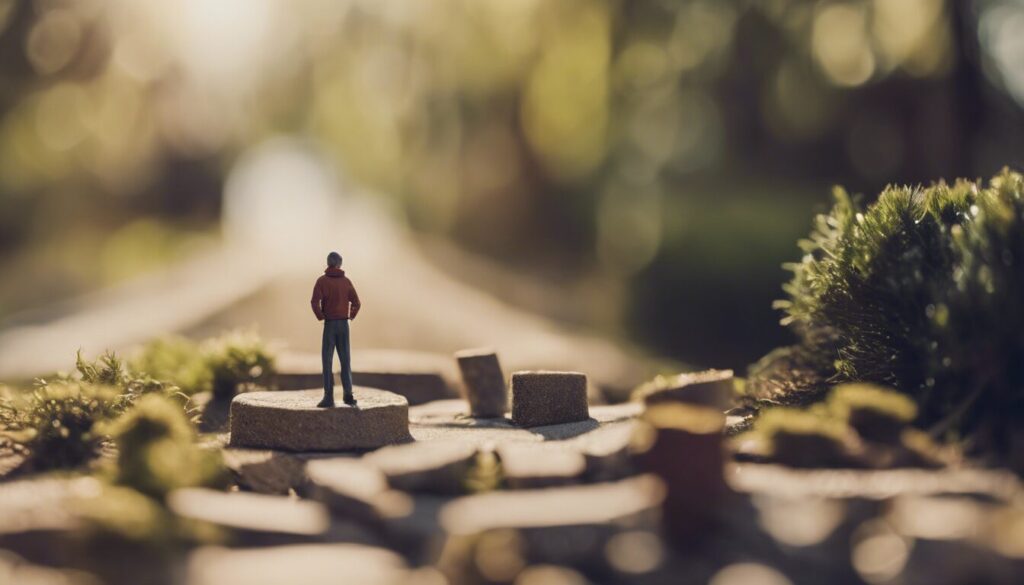
改善することで自分へのメリットはたくさんあります。
まず、スキルアップや知識の習得が挙げられます。
これにより、自分の価値が高まり、転職や昇進時に有利に働くでしょう。
また、改善活動を通して問題解決能力やコミュニケーション能力が向上します。
人間関係やチームワークがスムーズになり、職場環境が良くなることで、ストレス軽減や仕事の達成感も得られます。
さらに改善により、自分の仕事の効率化が図れることで、余裕を持った時間管理が可能になり、プライベートの充実にも繋がります。
最後に、評価を上げるためには、別記事で紹介している『会社からの評価を上げるには』にも繋がります。
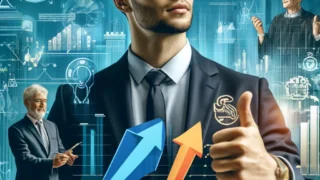
改善活動を通じて自己成長を図ることで、より良いキャリアを築くことができるでしょう。
改善を見つける方法
現代の企業において、日々の業務の中で多くの「めんどくさい」が発生します。
その原因は、効率的でない作業方法や煩わしい管理手続き、無駄な手間や時間がかかるプロセスなど、さまざまなことが考えられます。
このようなめんどくさいを解消することが、生産性向上や業務改善への道筋になります。
これからご紹介する改善方法を活用し、業務の効率化や品質向上を実現していきましょう。
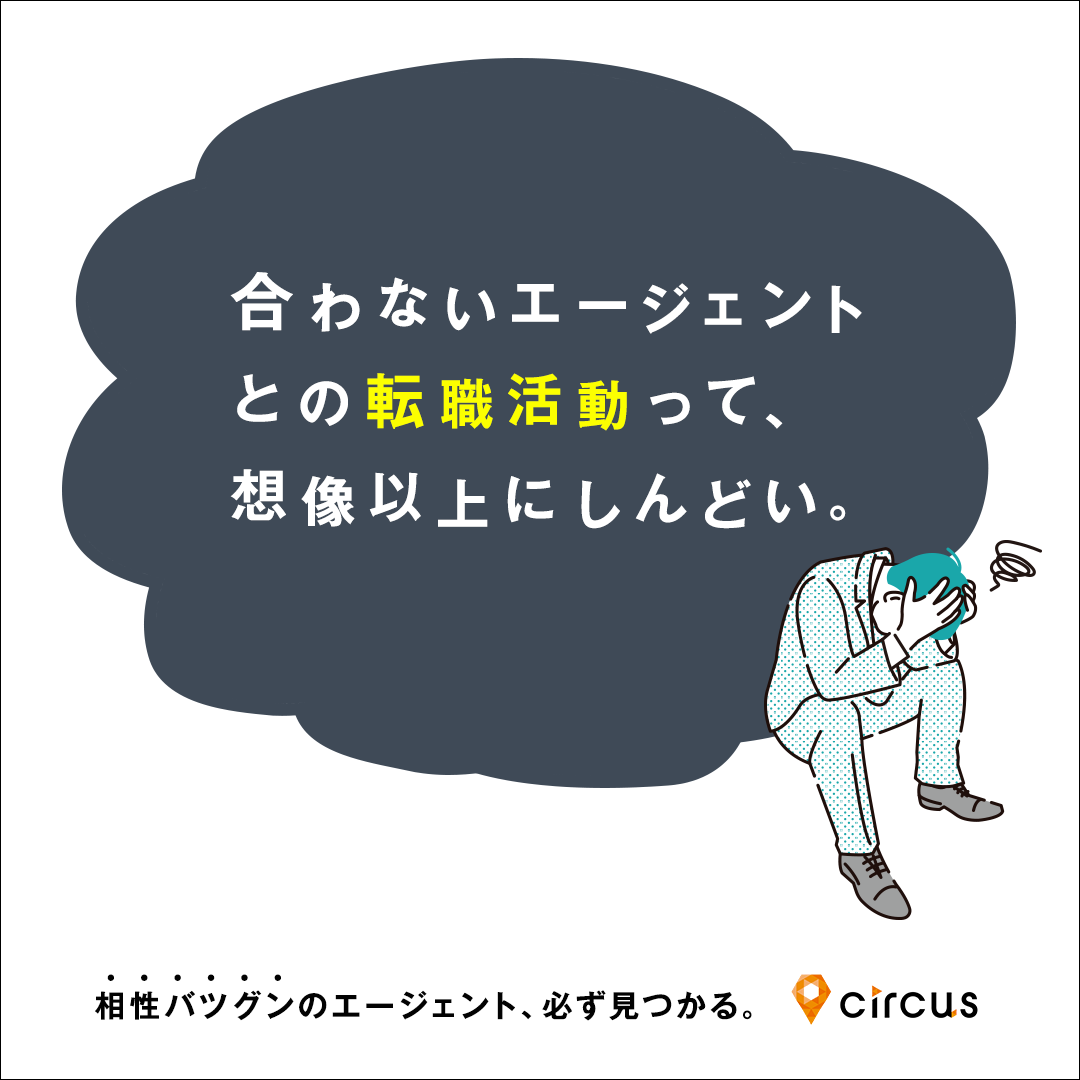
環境編(5S)
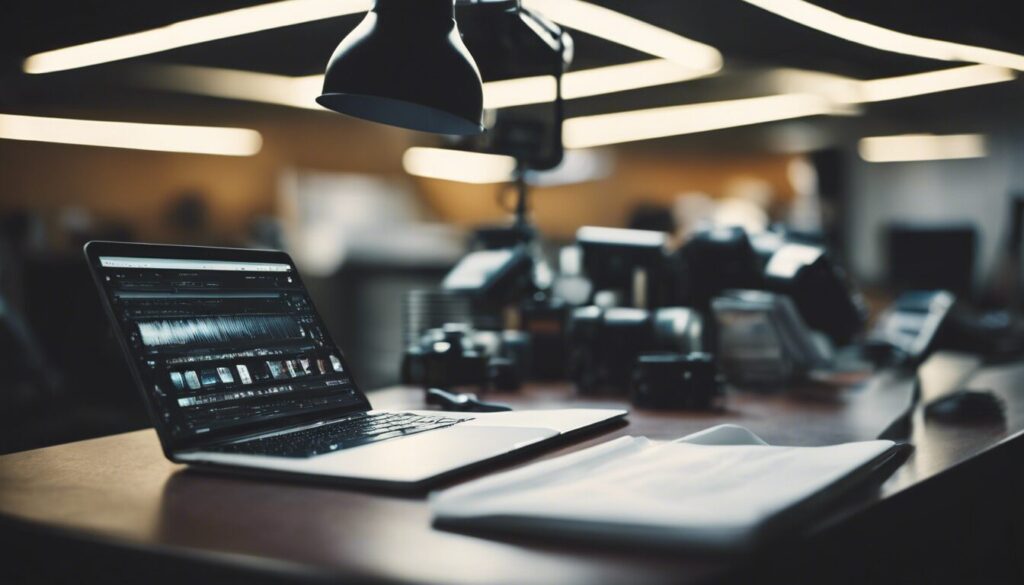
職場環境におけるめんどくさいを解消するためには、「5S」の観点から取り組むことが効果的です。
5Sとは、整理(Seiri)、整頓(Seiton)、清掃(Seiso)、清潔(Seiketsu)、躾(Shitsuke)の頭文字を取った言葉で、職場環境の改善と効率化を目指します。
まず整理では、不要なものを見極めて処分することが大切です。
必要なものだけを残し、整理整頓を容易にすることで、業務の効率化が図れます。
問題点
作業台に使うもの使わないものなどいろいろなものがあり必要なものを探すのにめんどくさい。
改善
必要なもの不要なものを整理し不要なものを捨て作業台には必要なものだけにした。
整頓では、定められた場所に物を戻し、すぐに使える状態に保つことが重要です。
作業スペースを確保し、必要なものがすぐに見つかる環境を整えることで、作業効率も向上します。
問題点
測定器など普段からよく使うものがいろいろな場所に置かれていて使いたい時に探すのがめんどくさい。
改善
測定器などの置き場所を決め、定位置化した。
清掃では、定期的に職場を掃除し、清潔な状態を維持することが求められます。
清潔な職場は、不具合やトラブル発生のリスクを低減し、品質向上に繋がります。
問題
設備のある一部がよく汚れ等で故障して修理にかなりの時間がかかってめんどくさい。
改善
定期的に清掃することにして故障の予防を行った。
清潔であり続けるためには、日々の清掃作業が欠かせません。
まずは自分の担当しているエリアから始め、社員同士で協力して職場全体を清潔に保ちましょう。
問題
エアコンや空調設備が汚れていて職場環境が悪くなり清掃する際に大幅な時間がかかりめんどくさい。
改善
定期的に業者に頼んだり自分たちで数分程度の掃除するようにして職場環境の悪化を防いだ。
最後に躾では、良い習慣やマナーを身に付け、継続的に5S活動を行うことが大切です。
継続的な取り組みが、職場環境の向上と業務改善の持続的な進化を生むでしょう。
問題
改善が一時的に終わってしまい問題が再発してしまっている為再度改善することがめんどくさい。
改善
習慣化出来る仕組み(管理表作成やルール)を作成して改善効果を継続出来るようにした。
結論として、5Sを取り入れた職場環境の改善は、業務効率向上や品質の向上、安全性の確保にも貢献し、多くのめんどくさいを解消する手段となります。
まずは今日からできることから始めて、着実に職場環境を改善していきましょう。
段取り編
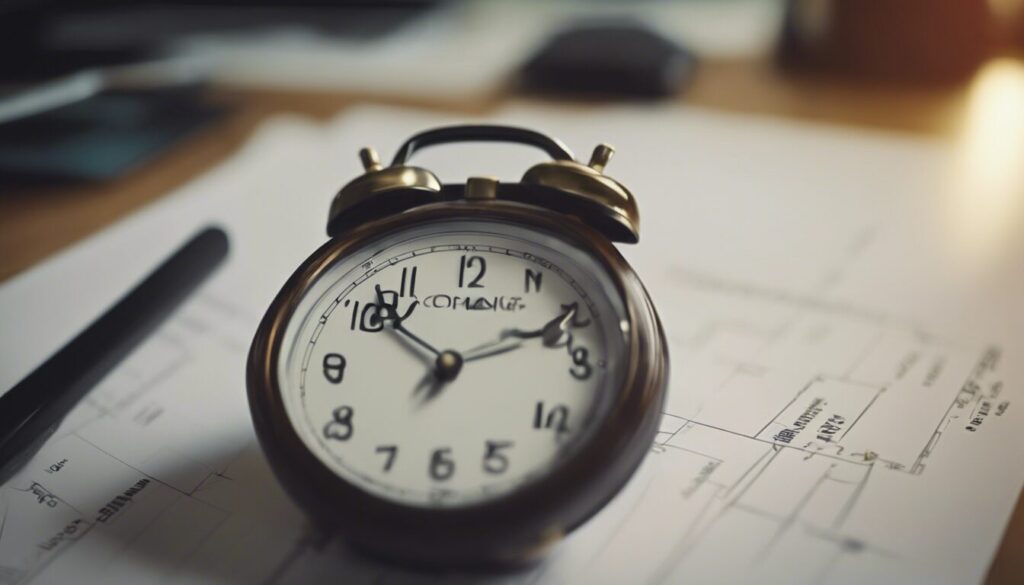
段取り作業は、生産効率向上や品質管理において重要なポイントです。
しかし、段取り作業が煩雑でストレスがたまることもしばしば。
そこで今回は、段取り作業におけるめんどくさい部分を改善する方法を紹介します。
まずは、現場の作業員の声をよく聞き、どの部分がめんどくさいと感じているかを把握しましょう。
次に、その原因を分析し、具体的な改善策を立案します。
例えば、以下のような取り組みが考えられます。
– 作業手順の見直し
問題
作業中に待ち時間が発生してしまい必要以上に時間がかかりめんどくさい。
改善
作業手順の見直しを行い待ち時間を無くし作業時間を削減した。
– 設備の改善
問題
加工する機械のスペックに合わない製品の為段取りにかなりの時間がかかりめんどくさい。
改善
加工する設備の見直しを行い適切な機械に振り分けを行った。
– マニュアルの整備
問題
手順書がなく段取り加工する際に毎回確認が必要でめんどくさい。
指導する際に毎回口頭で伝えているため何度も同じことを言わなければならないので指導する側も教わる側もめんどくさい。
改善
手順書を作成し確認作業や指導を楽にした。
– 社員教育の充実
そして、改善策を実行する際には、段階的に導入し、効果を検証しながら進めることが大切です。
また、定期的に改善活動を見直し、継続的に取り組んでいく姿勢が求められます。
最後に、現場の意識向上も大事なポイントです。
現場の作業員が、自ら改善意識を持ち、問題点を見つける力を身につけることで、より効果的な改善活動が展開できるでしょう。
社員と経営陣が共に意識を高め、常に最適な段取り作業を目指すことが大切です。
手作業編
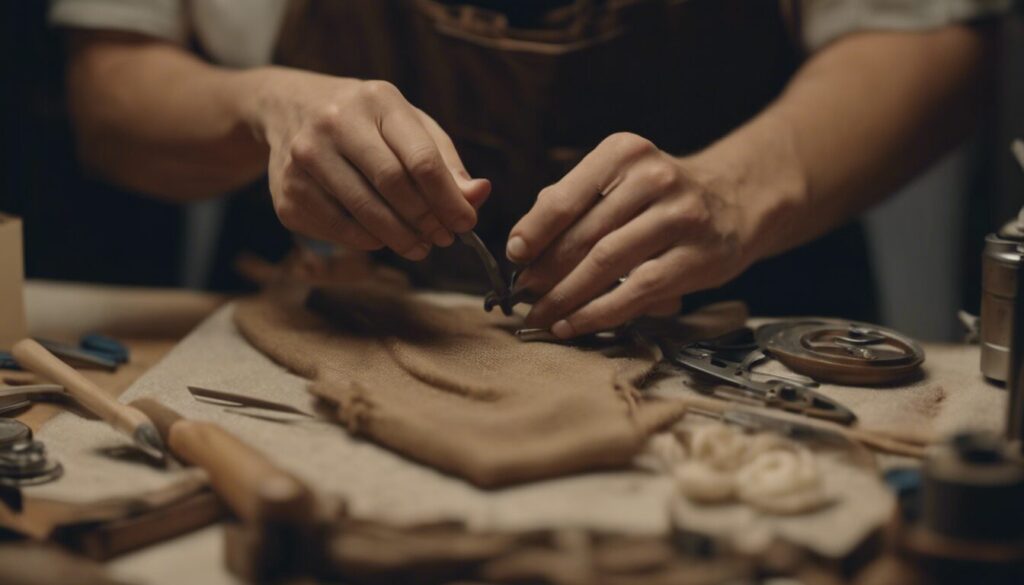
バリ取り作業などの手作業も、効率化が求められる業務のひとつです。
手作業におけるめんどくさい部分を改善する方法をいくつかご紹介します。
はじめに、作業効率を低下させている要因を見極めることが重要です。
例えば、以下のようなポイントをチェックしましょう。
– 作業方法の不適切さ
– 作業環境の問題
– 作業ツールの適用性
次に、それらの問題点に対して改善策を考案し、実行に移します。
具体的な改善策としては、作業方法の見直しや、環境整備、適切なツールの導入が挙げられます。
また、手作業を機械化することも、効率化や品質向上につながります。
例えば、バリ取り作業では、ロボットを活用した自動化が可能です。
導入コストが高くなることもありますが、長期的な効果を見越して検討する価値があります。
他には加工でバリ取りをする必要がないプログラムに編集し必要最低限の手作業にすることも重要です。
どちらかというと後者の方が現実的だと思いますので是非検討してみてください。
最後に、人材育成にも力を入れましょう。
手作業においては、スキルや経験が作業のクオリティに大きく関わります。
教育や研修を通じて、作業員のスキルを向上させることが、煩雑な手作業の改善に繋がります。
加工編
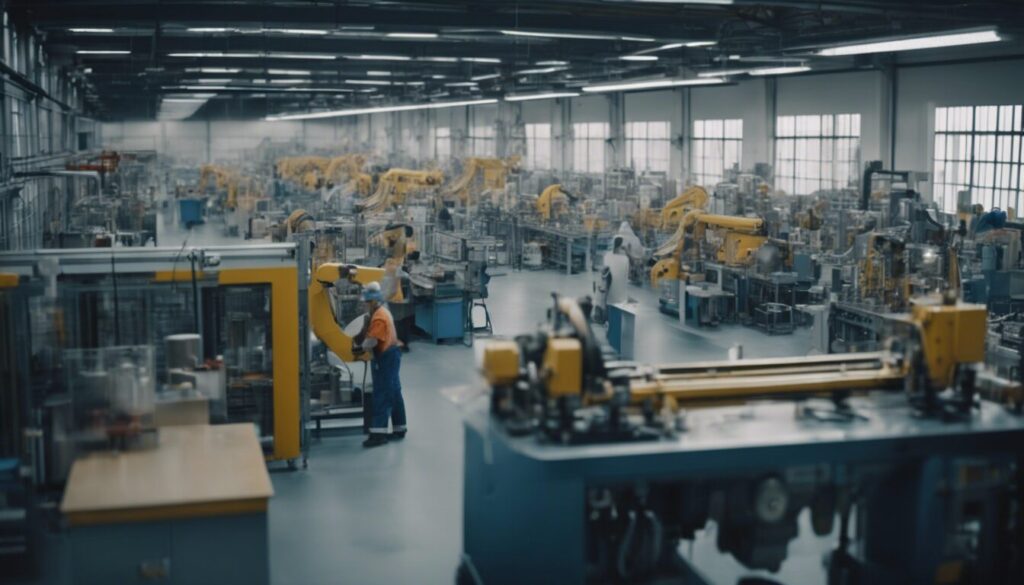
加工現場では、加工時間が短くて機械がすぐに止まってしまい、複数の作業に対応しきれずに困っていることがあります。
そのような状況を改善するためには、まずは現場で発生している問題を把握し、具体的な改善策を考えることが重要です。
例えば、次のような取り組みが考えられます。
– 現場の作業手順を見直し、無駄な動作を省くことで効率を向上させる。
-1ヶずつの加工から多数個取りで加工出来ないかを検討する。
– 機械のメンテナンスを徹底し、故障を未然に防ぎ、停止時間を短縮する。
– 作業者のスキルアップを図ることで、作業のスピードや品質を向上させる。
また、経営や管理の側からも、効率向上に取り組むことが求められます。
技術革新や設備投資を通じて、生産ラインの改善を図ることができます。
企業全体で加工現場の改善活動に取り組むことで、効果的な解決策が見つかる可能性もあります。
めんどくさいが見つかるけど改善方法がわからない場合
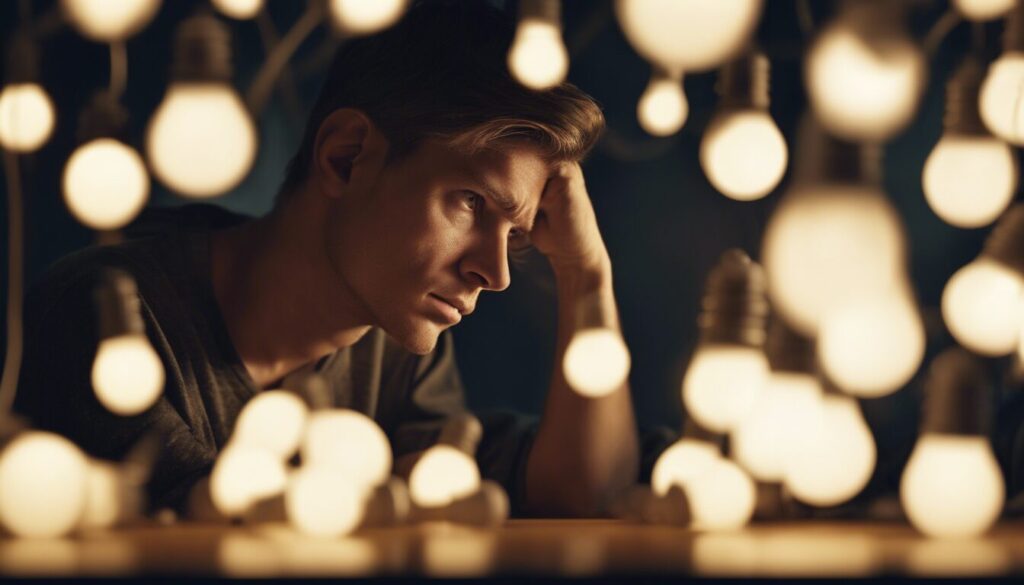
めんどくさい状況が見つかっても、どのように改善すべきかわからない場合があります。
そんなときには、上司や先輩に相談し、一緒に改善策を考えることが大切です。
彼らは経験豊富であり、過去の事例や知識を持っているので、新たな視点やアイデアを提供してくれることでしょう。
せっかくのめんどくさいが見つかったのに改善に繋げられず終わってしまってはもったいないです。
めんどくさいから何か変えれないかと考えることはとてもいいことなので自分の作業を楽にする、会社での評価を上げるという面でも是非、周りの人に相談するなどして生かしてください。
今は改善まで一人で出来なくても周りからの意見をもらうことで知識が付くのでいずれ自分だけでも改善に持っていけることが増えてきます。
大事なことは諦めずにやりきることです。
まとめ
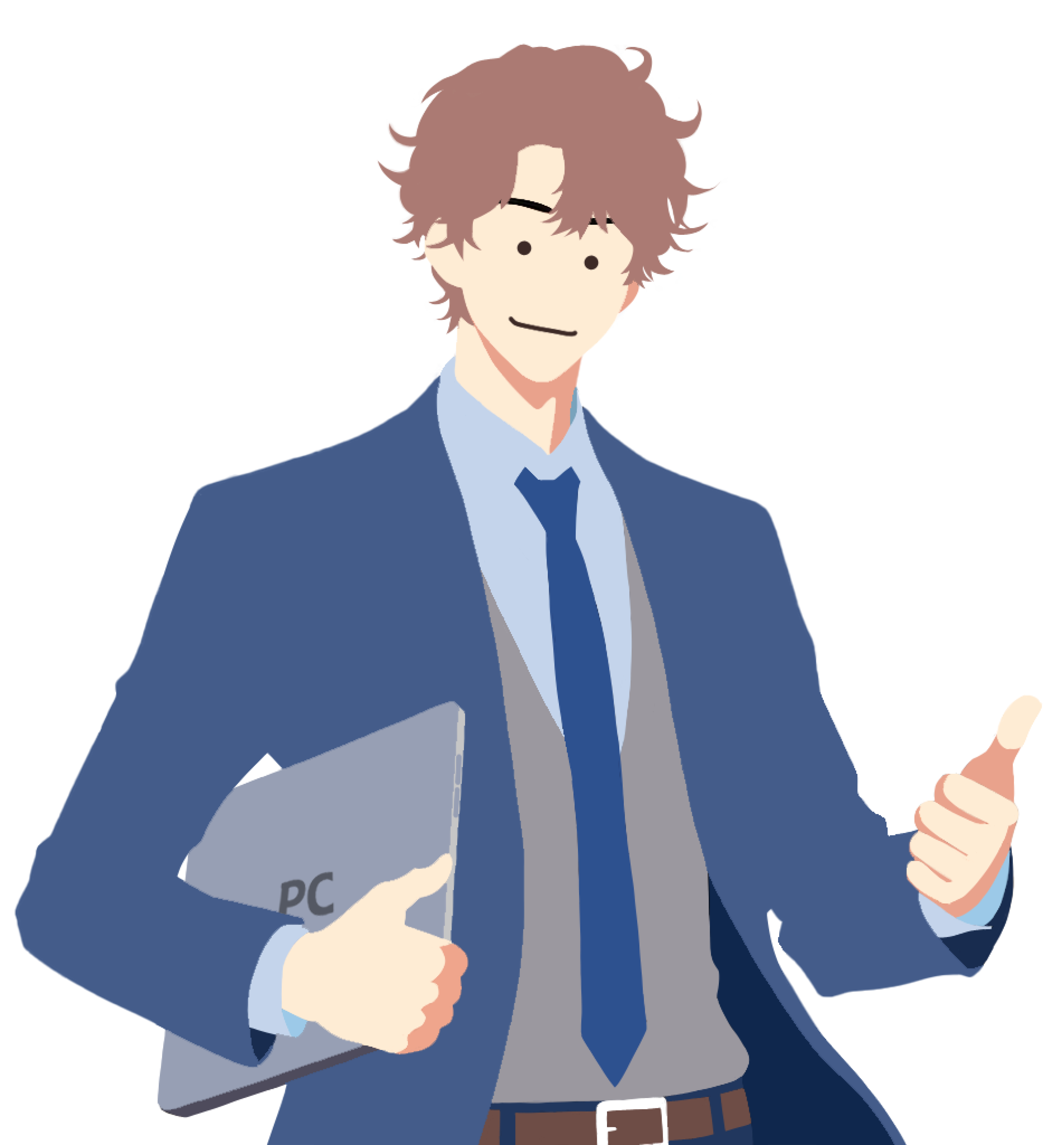
なんかたくさん改善出来そうな気がしてきた!
日頃のめんどくさいから改善に繋げてみる!
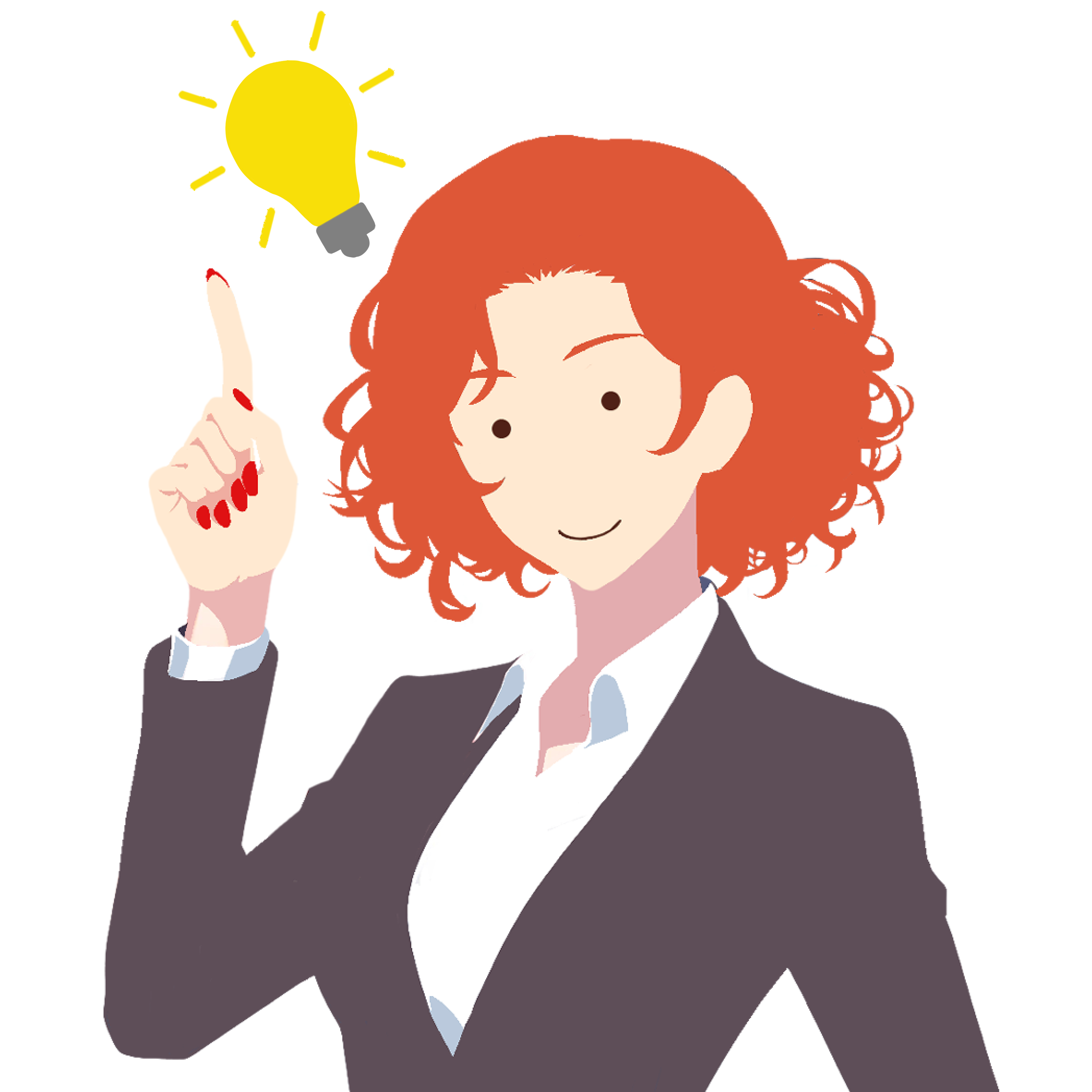
ちょっとしたことが改善に繋がります。
まずは小さいことから初めていきましょう。
加工現場の改善は、効率向上や品質向上に直結する重要な取り組みです。
具体的な改善策を見つける難しさがある場合でも、上司や先輩と連携して問題を解決しましょう。
また、根本原因に対処することで、効果的な改善が実現できるでしょう。
今回の記事を参考に、あなたも現場の改善に積極的に取り組んでください。
そして、次の一歩として、新たな問題や課題に取り組む意欲を持ち続けることが大切です。